Overview
Busbars for lithium batteries are critical conductive components used to connect battery cells within energy storage systems, ensuring efficient power distribution and minimizing energy loss. Made from highly conductive materials such as copper or aluminum, these busbars support high-current applications while reducing resistance and heat buildup. Reliable suppliers provide busbars in various sizes, shapes, and custom designs to meet the specific requirements of lithium battery packs used in electric vehicles, renewable energy systems, and portable electronics. Their precision engineering ensures optimal performance, durability, and safety in demanding energy applications.
Basic Information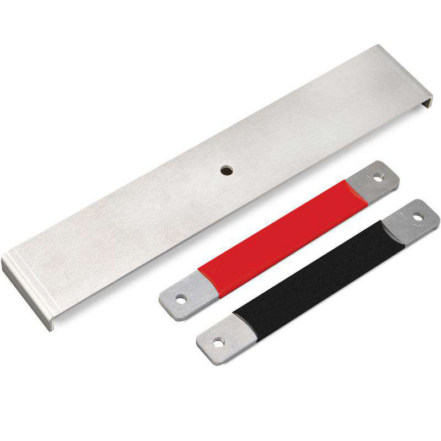
– Surface Treatment: Electroplating
– Forming Process: Metal Stamping Parts
– Surface Finish Options: Nickel Plating, Sn Plating, Tin Plating, Zinc Plating
– Sample Availability: Available
– Tolerance: ±0.001 mm
– Size: Customizable as per requirement
– Application: Industrial, Furniture, Automotive, Motorcycle, etc.
– Manufacturing Approach: Metal Stamping, Cutting, Punching, Bending, Welding
– Transport Packaging: OPP Bag, Box, or Custom
– Specification: Customized
– Origin: Xiamen, China
OEM Services for Metal Stamping Parts
– Custom Design: We offer tailored design services for OEM metal stamping parts, leveraging advanced CAD software to create designs that align with your specifications and industry standards.
– Material Sourcing: Select from a diverse range of high-quality metals and alloys suited to your application requirements. Our team ensures that the chosen materials meet durability and performance criteria.
– Tooling and Die Fabrication: We develop precision tooling and dies using state-of-the-art machinery, ensuring high accuracy and consistency in part production. Our tooling process is optimized for both efficiency and quality.
– Manufacturing Capabilities: Our advanced metal stamping equipment handles various production volumes, from prototypes to large-scale runs, delivering parts with precise dimensions and reliable performance.
– Surface Finishing: Enhance the functionality and aesthetics of your stamped parts with our surface finishing options, including electroplating, polishing, and coating, tailored to meet your specific requirements.
– Quality Assurance: Rigorous quality control procedures are in place to ensure each part meets stringent standards. We conduct comprehensive inspections and tests to guarantee consistency and reliability.
– Custom Packaging and Logistics: We provide customized packaging solutions and manage logistics to ensure your parts are delivered securely and on schedule, according to your needs.
– Comprehensive Support: From initial consultation to post-production support, our dedicated team provides ongoing assistance to ensure your satisfaction and address any concerns that arise.
Surface Treatments for Metal Stamping Parts
-
Electroplating
– Description: A process that deposits a layer of metal onto the surface of the part using an electric current. Commonly used for improving corrosion resistance and enhancing appearance.
– Types: Nickel plating, chrome plating, zinc plating.
-
Powder Coating
– Description: A dry coating process where powdered paint is electrostatically applied and then cured under heat. It provides a durable, high-quality finish with excellent resistance to scratches, chipping, and fading.
-
Anodizing
– Description: An electrochemical process that converts the surface of aluminum into a durable, corrosion-resistant layer. Anodizing also enhances appearance and can be dyed in various colors.
-
Plating
– Description: The application of a thin layer of metal to the surface of the part to improve wear resistance, reduce friction, or provide an aesthetic finish.
– Types: Tin plating, copper plating.
-
Spraying
– Description: A method where paint or protective coating is sprayed onto the part’s surface. This process is used for both aesthetic and protective purposes, offering a wide range of colors and finishes.
-
Oxidation
– Description: A chemical treatment that forms a protective oxide layer on the surface of metals, such as steel. It improves corrosion resistance and can provide a unique aesthetic finish.
-
Polishing
– Description: A mechanical process that smooths and shines the surface of the part. Polishing removes imperfections and enhances the visual appeal of the metal.
-
Sandblasting
– Description: A process that uses high-speed abrasive particles to clean or roughen the surface. It prepares the surface for further treatments or provides a textured finish.
-
Passivation
– Description: A treatment process that enhances the natural oxide layer on stainless steel to improve corrosion resistance. It involves soaking the part in a solution that removes free iron and other contaminants.
Reviews
There are no reviews yet.