Overview
Metal wire forming is a precision process used to bend, twist, and shape metal wires into specific configurations for a wide range of applications, from industrial machinery to consumer products. This process is typically performed using high-quality materials such as stainless steel, copper, or aluminum, ensuring strength, flexibility, and corrosion resistance. Expert manufacture of metal wire forming involves advanced techniques like CNC wire bending, coiling, and welding, allowing for highly accurate, custom designs. These components are used in industries such as automotive, electronics, and medical devices, providing reliable solutions for a variety of complex, high-performance needs.
Basic Information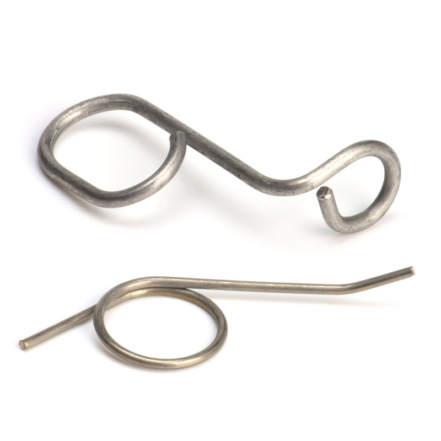
– Surface Treatment: Electroplating
– Forming Process: Metal Stamping Parts
– Surface Finish Options: Nickel Plating, Sn Plating, Tin Plating, Zinc Plating
– Sample Availability: Available
– Tolerance: ±0.001 mm
– Size: Customizable as per requirement
– Application: Industrial, Furniture, Automotive, Motorcycle, etc.
– Manufacturing Approach: Metal Stamping, Cutting, Punching, Bending, Welding
– Transport Packaging: OPP Bag, Box, or Custom
– Specification: Customized
– Origin: Xiamen, China
The Production Process for Our Metal Stamping Parts:
-
Order Receipt and Drawing Review
– Receive and review customer orders, including technical drawings in formats such as DXF, IGS, STEP, or PDF.
-
Design Confirmation
– Confirm design details with the customer to ensure accuracy before production begins.
-
Material Preparation
– Select and prepare metal sheets according to the required specifications.
-
Precision Cutting
– Utilize laser cutting and CNC shearing to cut metal sheets to precise dimensions.
-
Forming and Shaping
– Perform bending, punching, and stamping to achieve the desired shapes and features.
-
Welding and Riveting
– Join metal components using advanced welding techniques and riveting.
-
Surface Treatment
– Apply necessary surface treatments, including plating and spraying, to enhance durability and appearance.
-
Assembly and Quality Control
– Assemble the components and conduct rigorous quality checks to ensure adherence to specifications.
-
Packaging and Shipping
– Package finished parts securely and manage logistics for timely delivery to the customer.
-
After-Sales Support
– Provide ongoing support and address any post-delivery issues to ensure customer satisfaction.
Factory Show
We operate a comprehensive range of plants and equipment to ensure the highest quality production. Our facilities are equipped with 25 punch presses ranging from 25 tons to 300 tons, precision wire EDM machines, grinding equipment, welding and polishing tools, and ultrasonic cleaning systems.
In addition to our manufacturing capabilities, we offer a variety of metal plating processes to enhance the durability, appearance, and functionality of our metal stamping products. These include electroplating, zinc plating, nickel plating, chrome plating, and anodizing. Our state-of-the-art plating facilities ensure consistent finishes, corrosion resistance, and compliance with industry standards.
This combination of professional and automated production lines, advanced mechanical equipment, rigorous quality control measures, and high-quality plating processes ensures we deliver metal stamping products of the highest standard.
Reviews
There are no reviews yet.