Precision Metal Stamping for Custom Component Parts
Top Metal Stamping offers efficient progressive die stamping with high-quality craftsmanship and precision tools for strict tolerances.
When it is determined that progressive die stamping is the most suitable manufacturing process for your component, Top Metal Stamping has the power stamping capability to produce strip materials ranging from 0.05mm to 2.5mm thickness and up to 150mm width. To ensure excellent product quality, we rely on experienced professionals who have been internally certified and verified in the design and production of progressive molds. Taking into account extremely stringent tolerance standards and understanding the need for precision metal components and high consistency, we use AutoCAD and SOLIDWORKS software for equipment development, along with advanced wire cutting machinery and CNC milling machines for product processing.
What is Progressive Die stamping?
Progressive stamping is a metal fabrication technique involving bending, punching, and coining processes to modify raw metal material. Quality Stamping & Tube specializes in progressive stamping and die manufacturing, offering precision metal stamping services and additional value-added options. They are a reliable source for high-quality finished stamped metal parts. Progressive dies consist of multiple moving components that require precise timing based on specific stamping requirements and material thickness for proper functioning. This technique is commonly used in industries like automotive, electronics, and appliances to efficiently manufacture simple or complex parts in large volumes. The process involves feeding flat sheet metal into an automatic feeding system within a stamping press, performing various operations at each station according to predetermined specifications, and separating the finished part from the strip stock after processing by the stamping die. Progressive metal stampings offer automation advantages through an assembly line approach until achieving the final form using metallic substrate as the base material
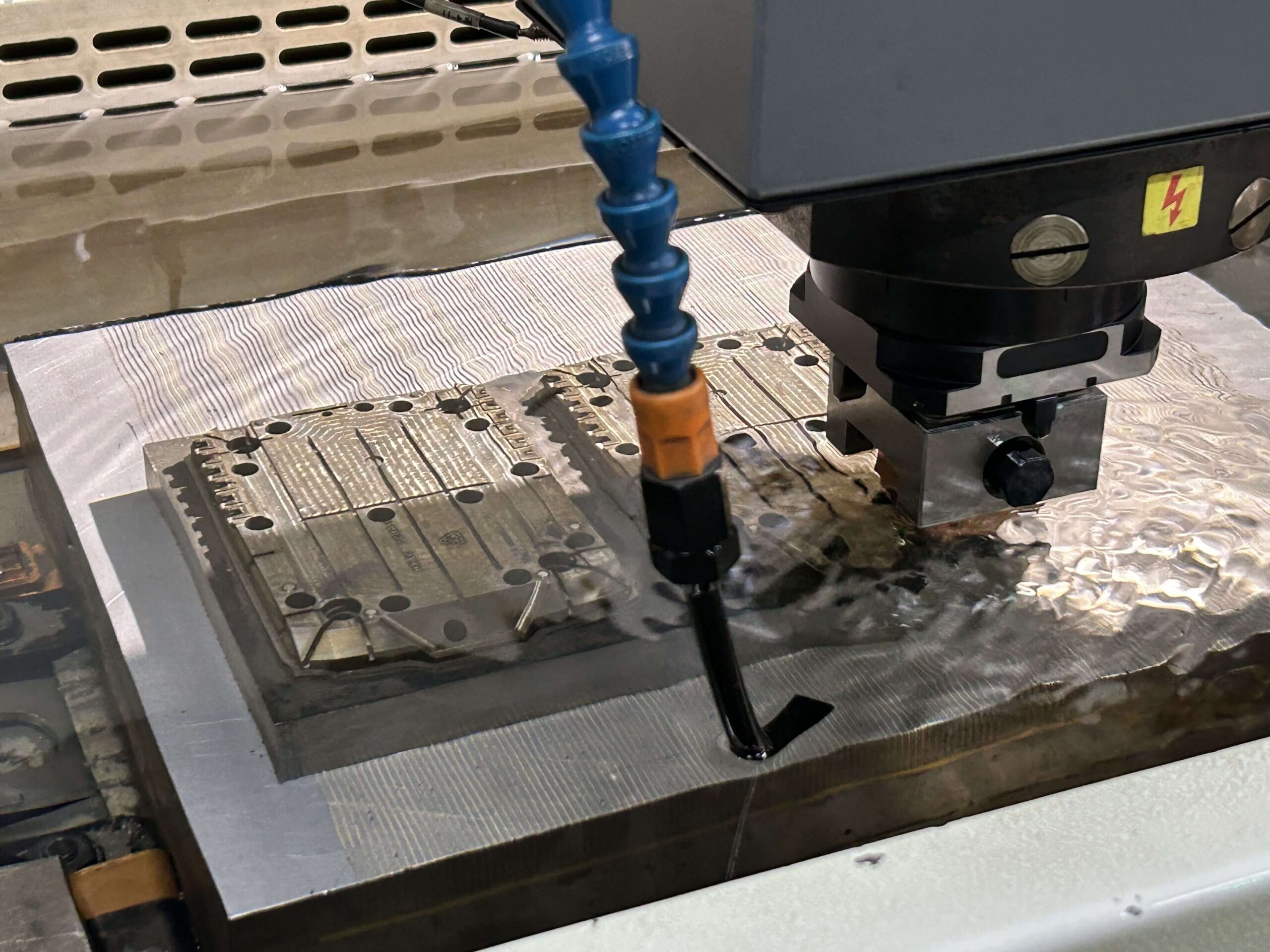
Advantages of Using Progressive Die Stamping
Progressive die stamping offers numerous benefits when compared to other traditional manufacturing methods. Progressive die advantages include:
Faster Production Speeds. Due to the continuous supply of materials, a continuous stamping machine can operate at extremely high speeds, providing the shortest cycle time for each part in mass production. This makes the cycle time more efficient, shortens delivery times and increases production capacity. For enterprises pursuing high-capacity production, this is particularly advantageous.
Less Scrap Material. The utilization of advanced die metal stamping provides a highly cost-effective material option for the production of parts, encompassing various techniques such as punching, stamping, bending, and other methods to modify the metal in order to achieve the desired final shape. Consequently, minimal scrap is generated during this process. Furthermore, the optimized design of the stamping die enables a significant reduction in waste.
Broader Design Freedom. Progressive die stamping offers broader design freedom. The process can accommodate numerous geometries, ranging from simple to complex.
Greater Production Capacities. Progressive die stamping can increase production capacity and shorten manufacturing time. The use of progressive stamping under continuous feeding also enables long production runs. Longer material change intervals mean more parts are completed in less time
Higher Rates of Repeatability. The progressive stamping equipment uses hard, high-quality tooling to achieve mass production while maintaining mold quality. This results in a high-quality, repeatable end product that can withstand continuous stamping runs without degradation, ensuring high quality parts and uniformity throughout the production process
Lower Cost Per Part. When using progressive die stamping technology, overall production costs are reduced due to reduced waste generation, faster setup, higher repeatability and increased production speed. Automated processes reduce the risk of injury in the workplace and significantly reduce labor costs, reducing the number of employees required to manufacture parts. All of these factors help reduce your total cost. The ability to produce robust parts efficiently and quickly
Quick Setup: With the improvement, the production of complex parts using progressive stamping technology requires only one installation, avoiding the multiple installation, tool and die changes in the traditional short-range stamping method. Because we design and manufacture in-house, we have the flexibility to adapt and quickly integrate modifications as engineering changes occur
Complex Geometry: Creation of parts with complex geometries is possible by the building nature of the die stations in a progressive tool. This process offers increased precision when compared to many other in-press operations, while maintaining optimal accuracy and precision.
Quality Assurance. We use a stringent Production Part Approval Process (PPAP) for all operations, including Failure Mode and Effects Analysis (FMEA), material requirements planning, Advanced Production Quality Planning (APQP), bar coding, and in-die protection to maintain the lowest possible defect rates on every production run.
Learn More about Our Metal Stamping Services and Capabilities
Equipment | Multiple presses with various shapes and sizes From 5 to 300 tons Multiple openings, beds, strokes, and speeds Latest technology feeders to handle material of any weight |
Capabilities | Stainless steel between 7 and 30 gauge Tolerances to 0.05mm Single and progressive dies State-of-the-art die and tool shop with EDM capabilities |
Top Metal Stamping specializes in working with various grades of carbon and alloy tool steels, such as powder steels, carbides, and high-speed steels. With our wire electrical discharge machining (EDM), CNC machining, we deliver highly accurate prototypes within tight tolerances and can efficiently handle large-scale production runs. Our in-house engineers meticulously oversee and optimize every aspect of the die design process to minimize waste and turnaround time, all while adhering to the ISO 9001:2015 and IATF16949 certified quality management systems we have in place.
Progressive Die Stamping Process
Progressive die stamping is a manufacturing process that involves cutting and forming metal parts using a die with multiple stamping stations. Here's a breakdown of the process:
Tooling Creation: Skilled toolmakers create the die set, which contains all the necessary tools for production, based on the specific application requirements.
Die Placement: Once created, the die is placed into the stamping press. It opens as the press moves up and closes as the press moves down.
Workpiece Loading: The workpiece is loaded into the die and moves through it while open, incrementally fed with each press stroke.
Operations: Each station in the die performs various operations such as embossing, coining, bending, cutting, etc., on the workpiece as it progresses through the die.
Part Ejection: Finished parts are ejected from the die after passing through each workstation, and they can be cut from the carrier strip.
The process relies on equipment such as servo press feed technology to push metal strips through the die's stations. Each station performs specific operations until a finished part is produced. The final station cuts the finished part from the carrier strip, treating the leftover metal as scrap. Progressive stamping dies are complex and require precise alignment to ensure proper timing and interaction of tools, pads, and carriers.
Progressive Stamping Materials
The progressive die stamping process is suitable for use with a wide range of materials, such as:
Aluminum
Steel
Stainless Steel
Brass
Copper
Inconel
Noble Metals
Coated Metals
Titanium
Tolerance
The Tolerance of Metal Stampings
The tolerance range for metal stampings typically varies based on specific design requirements and application needs. Tolerance refers to the permissible deviation in dimensions during the manufacturing process to ensure the quality and functional requirements of the parts.
In metal stampings, controlling tolerances is crucial to maintaining product quality and performance. Here are some common examples of tolerance ranges:
Dimensional Tolerance: Dimensional tolerance refers to the allowable deviation in dimensions such as length, width, thickness, etc., of the parts. For example, for a part with a length of 100mm, the dimensional tolerance can be ±0.1mm, indicating an allowable deviation range of 99.9mm to 100.1mm.
Flatness Tolerance: Flatness tolerance measures the levelness of the part's surface. It describes the maximum distance between the part surface and an ideal plane. For example, the flatness tolerance can be 0.1mm, indicating a maximum distance of 0.1mm between the part surface and the ideal plane.
Parallelism Tolerance: Parallelism tolerance describes the deviation between parallel surfaces of the part. It measures the maximum difference in distance between the parallel surfaces. For example, the parallelism tolerance can be 0.05mm, indicating a maximum distance difference between the parallel surfaces of 0.05mm.
Roundness Tolerance: Roundness tolerance measures the roundness deviation of circular parts. It describes the maximum distance between the curve around the circular part and an ideal circle. For example, the roundness tolerance can be 0.03mm, indicating a maximum distance between the curve around the circular part and the ideal circle of 0.03mm.
These tolerance ranges are just examples, and actual tolerances should be determined based on specific design requirements and application needs. During the design process, factors such as part functionality, assembly requirements, and manufacturing feasibility need to be considered to determine the appropriate tolerance ranges.
Applications
Progressive die stamping offers a wide range of benefits, including long run lengths, cost-effectiveness, fast production, short setup times, decreased labor costs, minimal scrap, and more. This process’ ability to efficiently produce parts in large volumes makes it a popular choice for several industries and applications, including:
Aerospace
Automotive
Medical Devices
Commercial Lighting
Electrical Distribution
Renewable Energy
MEP Applications
Mining
Appliances
Sporting Goods
Food & Beverage
Quality Control
Quality control is a critical aspect of our metal stamping service, and we take utmost care to ensure that every product we manufacture meets the highest standards of quality and precision. Our quality control process is rigorous and covers various stages of production, from initial design to final inspection. Here's how we implement quality control in our metal stamping service:
Design Review: We start by conducting a thorough design review to ensure that the product design meets the required specifications and standards. Our team of experienced engineers examines the design for any potential issues or improvements that can be made to enhance product performance.
Material Selection: We use only high-quality materials sourced from reputable suppliers. Our materials undergo stringent testing to ensure they meet the necessary mechanical and chemical properties for the specific application.
Advanced Machinery and Technology: We utilize state-of-the-art stamping equipment and technology in our manufacturing process. Our machines are regularly calibrated and maintained to ensure accurate and consistent results.
In-Process Inspection: Throughout the stamping process, we conduct in-process inspections to monitor the quality of each component as it is being manufactured. This allows us to detect and address any deviations or defects promptly.
Dimensional Accuracy: We employ precision measuring instruments to verify the dimensional accuracy of each stamped part. This ensures that the final product conforms to the required specifications.
Surface Finish and Coatings: We pay close attention to the surface finish of the stamped components. Depending on the application, we may apply various coatings or treatments to enhance durability and corrosion resistance.
Final Inspection: Before shipping, each batch of stamped products undergoes a comprehensive final inspection. Our quality control team examines the parts for any defects, ensuring that they meet all customer requirements.
Traceability and Documentation: We maintain meticulous records of the entire production process, including material certifications, inspection reports, and other relevant documentation. This ensures full traceability and transparency in our quality control procedures.
Our commitment to quality control has earned us a reputation for delivering reliable and high-quality metal stamped components to our customers. We continuously strive for continuous improvement, investing in training, and upgrading our equipment to stay at the forefront of quality manufacturing.