Surface Treatment Options:
1.Anodization
Enhances aluminum’s natural oxide layer for improved corrosion resistance and wear properties, available in various colors.
2.Powder Coating
Durable finish resistant to chips, scratches, and fading, offering extensive color and texture choices.
3.Electroplating
Deposits metal layers like nickel, zinc, or chrome to enhance appearance, corrosion resistance, and surface hardness.
4.Passivation
Chemical treatment to boost corrosion resistance without altering appearance.
5.Polishing
Creates a smooth, reflective surface for improved aesthetics.
6.Brushing
Uniform satin texture that hides fingerprints and minor scratches.
7.Painting
Customizable colors and protective coating.
8.Sandblasting
Creates a textured finish for enhanced adhesion and unique appearance.
Materials and Customization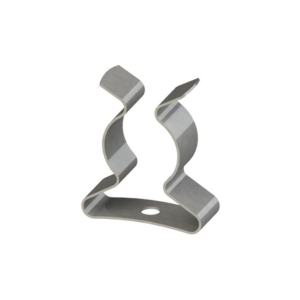
Materials: Carbon spring steel, alloy spring steel, stainless spring steel,plastic (nylon or polypropylene), rubber-coated metal
Customization: Sizes and dimensions can be tailored according to customer requirements
Applications: Network devices, communication equipment, computers, household appliances, distribution systems, educational toys, among others
Quality Control Process for Metal Stamping
- Incoming Material Inspection
– Description: Evaluate raw materials for compliance with specifications and quality standards before production. This includes testing material properties such as thickness, hardness, and chemical composition.
- Pre-Production Sampling
– Description: Conduct initial trials and inspections on pre-production samples to ensure that the stamping process and tooling produce parts within the required tolerances and quality levels.
- In-Process Monitoring
– Description: Implement continuous monitoring during production to ensure that the stamping process remains consistent. This includes checking for defects like warping, misalignment, and dimensional accuracy.
- Dimensional Inspection
– Description: Use precision measuring instruments such as calipers, micrometers, and CMMs (Coordinate Measuring Machines) to verify that parts meet specified dimensions and tolerances.
- Functional Testing
– Description: Test parts for proper functionality, ensuring they meet the required performance criteria. This may include checks for fit, alignment, and operational integrity.
- Surface Quality Inspection
– Description: Inspect the surface finish of parts for defects such as scratches, dents, or coatings issues. This includes visual inspections and using tools to assess surface texture and coating integrity.
- Post-Production Testing
– Description: Conduct additional tests on completed parts, including stress and load tests, to confirm durability and reliability under real-world conditions.
- Final Inspection and Approval
– Description:After stamping, the parts undergo a final inspection where dimensions, surface finish, and overall quality are checked to ensure they meet customer specifications.Approve or reject parts based on this thorough evaluation.
- Documentation and Traceability
– Description: Detailed records of all inspections and tests are maintained for traceability. These records include information about the material, process parameters, and inspection results.Any parts that do not meet quality standards are documented in a non-conformance report (NCR), and corrective actions are taken to address the root cause.
- Feedback and Continuous Improvement
– Description: Data from quality inspections and customer feedback is used to continuously improve the stamping process. Any recurring issues are analyzed, and process improvements are implemented to enhance quality.
Reviews
There are no reviews yet.