Overview
Unistrut brackets are essential components used in structural support systems, designed to connect and secure Unistrut channel frames in various construction, electrical, and mechanical applications. These brackets are manufactured from durable materials like stainless steel or galvanized steel to ensure strength, corrosion resistance, and long-lasting performance. The manufacturing process involves precision cutting, bending, and finishing to meet industry standards, enabling reliable and efficient installations. Unistrut brackets come in various shapes and sizes, providing flexible solutions for mounting, bracing, and supporting loads in commercial and industrial projects.
Basic Information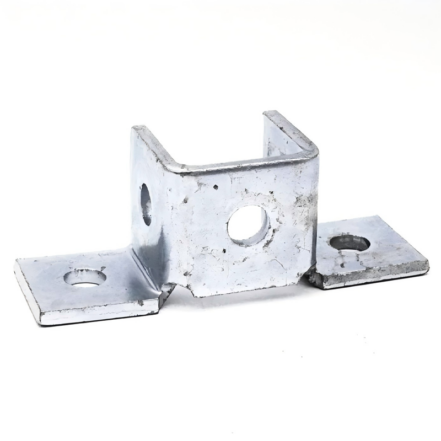
– Surface Treatment: Electroplating
– Forming Process: Metal Stamping Parts
– Surface Finish Options: Nickel Plating, Sn Plating, Tin Plating, Zinc Plating
– Sample Availability: Available
– Tolerance: ±0.001 mm
– Size: Customizable as per requirement
– Application: Industrial, Furniture, Automotive, Motorcycle, etc.
– Manufacturing Approach: Metal Stamping, Cutting, Punching, Bending, Welding
– Transport Packaging: OPP Bag, Box, or Custom
– Specification: Customized
– Origin: Xiamen, China
Quality Control Process for Metal Stamping
-
Incoming Material Inspection
– Description: Evaluate raw materials for compliance with specifications and quality standards before production. This includes testing material properties such as thickness, hardness, and chemical composition.
-
Pre-Production Sampling
– Description: Conduct initial trials and inspections on pre-production samples to ensure that the stamping process and tooling produce parts within the required tolerances and quality levels.
-
In-Process Monitoring
– Description: Implement continuous monitoring during production to ensure that the stamping process remains consistent. This includes checking for defects like warping, misalignment, and dimensional accuracy.
-
Dimensional Inspection
– Description: Use precision measuring instruments such as calipers, micrometers, and CMMs (Coordinate Measuring Machines) to verify that parts meet specified dimensions and tolerances.
-
Functional Testing
– Description: Test parts for proper functionality, ensuring they meet the required performance criteria. This may include checks for fit, alignment, and operational integrity.
-
Surface Quality Inspection
– Description: Inspect the surface finish of parts for defects such as scratches, dents, or coatings issues. This includes visual inspections and using tools to assess surface texture and coating integrity.
-
Post-Production Testing
– Description: Conduct additional tests on completed parts, including stress and load tests, to confirm durability and reliability under real-world conditions.
-
Final Inspection and Approval
– Description: Perform a comprehensive final inspection before shipping, ensuring that all parts meet quality standards and specifications. Approve or reject parts based on this thorough evaluation.
-
Documentation and Reporting
– Description: Maintain detailed records of quality control inspections and tests. Document any defects or non-conformance issues and report them for corrective actions.
-
Feedback and Continuous Improvement
– Description: Review quality control data to identify trends and areas for improvement. Implement corrective actions and process improvements to enhance overall product quality and efficiency.
Quality Documentation
- ISO 9001:2015 Certification
- IATF 16949 Certification
- First Article Inspection (FAl)
- PPAP Report(Production Part Approval Process)
- Material Technical Data Sheets (TDS)
- CMM Inspection Report
- SPC Report (Statistica Process Control)
- Material Certificates
- Dimensional Inspection Report (CMM)
- DFM feedback
Reviews
There are no reviews yet.